BLOG

Análisis De La Imagen Para La Dureza
La prueba de dureza es una característica fundamental en el análisis de las propiedades de los componentes y, como importante herramienta de prueba de materiales, este parámetro crítico puede ser realizado y medido por una multitud de métodos y técnicas.
Mientras que algunos tipos de prueba de dureza tales como la prueba de Rockwell darán resultados rápidos, de un solo proceso basados en la profundidad de indentación, muchos de los tipos de prueba comúnmente utilizados, tales como Vickers, Knoop y Brinell, requieren un proceso secundario para determinar el tamaño de la sangría. Estos procesos secundarios pueden consumir mucho tiempo, son ineficientes y propensos a errores subjetivos. Uno de los medios para mejorar la productividad al tiempo que proporciona consistencia al proceso es a través de la sangría automática y la lectura de impresiones utilizando el análisis de imágenes. Mejoras dramáticas en los últimos años en hardware, electrónica, algoritmos de imagen y capacidades de software han abierto la puerta a procesos de prueba extremadamente precisos y confiables que proporcionan resultados más rápidamente que nunca. Estas técnicas están mostrando una gran promesa de aumentar la eficiencia, velocidad y precisión a niveles nunca alcanzados antes.
Prueba de dureza automática
Dos de las pruebas de dureza más comunes son Knoop y Vickers, usadas en pruebas micro y macro para determinar la dureza del material basado en la medición del tamaño de una impresión en forma de diamante dejada por una aplicación de una fuerza especificada. La naturaleza de la prueba típicamente dicta una fuerza relativamente ligera, dando como resultado impresiones extremadamente pequeñas que deben medirse a nivel de micrómetros. Las técnicas tradicionales, todavía ampliamente practicadas hoy en día, involucran microscopios con objetivos de resolución variable integrales al probador de dureza, que miden manualmente a través de un ocular basado en la interpretación humana. Previsiblemente, esto es lento, ineficiente, y en el ritmo acelerado de hoy, el ambiente extremo, cada vez más inaceptable. No es infrecuente que un técnico produzca y mida por ojo centenares de indentaciones durante un día, con la fatiga probablemente comprometer el proceso de la medida mientras que los hilos aumentan en cantidad. A esto se añade la necesidad de realizar un análisis completo de una travesía de dureza que consiste a menudo en más de 15 sangrías cada una, usualmente varias veces en una sola muestra, y se hace evidente la necesidad de técnicas automáticas avanzadas.
En los últimos años y cada vez más en el futuro, estos procesos manuales han seguido y seguirán dando paso rápidamente a la automatización en todos los aspectos del proceso. Se están desarrollando nuevas técnicas en la preparación de materiales, el movimiento en escena, la interpretación y análisis de resultados, e incluso la presentación de informes. Una tecnología de este tipo que se está implementando en muchos laboratorios de todo el mundo es el desplazamiento automático de escenarios y el análisis de imagen de las indentaciones Knoop, Vickers y Brinell.
Un sistema automático de dureza consta típicamente de un probador completamente controlable, que incluye una torreta auto-rotativa o giratoria y accionamiento en el eje Z, ya sea desde la carcasa del cabezal / indentador o desde un sistema accionado por husillo para aplicar tanto la indentación a una fuerza predeterminada como Como para enfocar la muestra. Añadir a esto un ordenador de sobremesa o portátil con software de dureza dedicado instalado, un XY automático que atraviesa escenario motorizado, y una cámara de vídeo USB, y el resultado es un sistema de prueba de dureza potente y totalmente automático. Después de la configuración inicial con muestras y un programa almacenado, se puede dejar solo para hacer automáticamente, medir e informar sobre un número casi ilimitado de travesías de indentación.
La tecnología más reciente elimina gran parte del hardware que en el pasado causó desafíos operacionales y espacio de trabajo desordenado. Por ejemplo, la etapa se mueve a través de un joystick virtual, y en algunos sistemas, los controladores de etapa se integran en la carcasa de la etapa. Los avances en algoritmos de movimiento de escenario y diseño mecánico han hecho la precisión XY y la repetibilidad mejor que nunca, que son fundamentales en los requisitos de recorrido de precisión como el análisis de profundidad de caso.
Análisis de imagen
El análisis de imágenes no es nuevo, pero la tecnología sigue avanzando, mejorando dramáticamente el proceso. Por ejemplo, la tecnología de la cámara ha evolucionado desde grabber de marco, a IEEE Firewire, a USB, eliminando el hardware adicional mientras que al mismo tiempo aumenta la resolución de la cámara y las posibilidades del campo de visión. Las capacidades de las cámaras actuales y en desarrollo, junto con la capacidad de procesamiento de las computadoras de hoy en día y los paquetes de software de mejora continua, han mejorado significativamente la precisión, repetibilidad y fiabilidad de la lectura automática de sangría. Todas las cámaras digitales tienen matrices de píxeles. Cada píxel puede estar activado o desactivado. Si se proyecta una imagen en blanco y negro en la matriz de píxeles, los píxeles de las áreas oscuras se apagarán y los de luz se encenderán. Contando el número, se puede determinar el tamaño de la mancha oscura en la imagen y posteriormente el área de la imagen. El tamaño de cualquier sangría se utiliza en combinación con el indentador y la fuerza aplicada para determinar el valor de dureza.
Travesía automática
La expansión de la productividad aún más es la capacidad de utilizar etapas XY de mayor tamaño capaces de contener dos, cuatro o incluso seis muestras a la vez en una serie de tipos de fijación. Las tramas preprogramadas y guardadas se abren, las muestras se alinean en los soportes y, con un solo clic, se inicia la indentación, lectura y notificación de una multitud de travesías en cada muestra. Autofocus mitiga cualquier problema de claridad indent debido a la variación de la posición Z. Un software más nuevo incluso permite diferentes escalas, fuerzas y objetivos de microscopio, dentro y entre travesías.
Las pruebas automatizadas también son cada vez más beneficiosas para las pruebas de dureza de Rockwell, en particular en los requisitos de patrones repetitivos, como las pruebas Jominy, en las que una serie de barras pueden ser probadas y reportadas, no tripuladas después de un clic del ratón.
Otras aplicaciones
Al igual que en las pruebas Knoop y Vickers, Brinell Testing por naturaleza es un proceso intensivo de mano de obra y manual que, en su estado convencional, requiere constante intervención humana y procesamiento. Dado que la prueba Brinell tradicional consiste en una sola fuerza de prueba controlada hecha con una bola de carburo de tungsteno de diámetro especificado, la impresión resultante debe medirse ópticamente (diámetro en mm) para determinar la dureza del material. Esto se realiza típicamente usando un microscopio manual de baja potencia, un proceso que es laborioso y subjetivo. Como en Knoop y Vickers, los errores inducidos por la fatiga de realizar mediciones repetidamente son comunes, y el proceso en sí puede ser ineficiente y lento. Con muchos procesos que requieren un 100% de inspección y productividad dependiendo del retorno rápido de los resultados, no es ninguna sorpresa que un medio para acelerar tanto el proceso como para mitigar los posibles errores inducidos manualmente esté en demanda. El método que puede ser más aplicable depende de una variedad de factores, incluyendo el requisito de tiempo de prueba, la geometría de la muestra, la técnica de carga y descarga, las propiedades del material, los requisitos de las normas ASTM y la adhesión y, por supuesto, la alineación presupuestaria.
Cuando se utiliza un probador de suelo o banco Brinell convencional que realiza la parte de sangría de la prueba solamente, una alternativa al proceso manual manual implica el uso de una cámara digital de mano que puede medir el diámetro de la impresión automáticamente usando análisis de imagen Técnicas. Como resultado, se ha vuelto relativamente fácil medir los sangrillos de Brinell a través de una cámara. Si falta un sistema de imagen manual que requiera intervención manual, entonces un sistema Brinell óptico totalmente automático puede proporcionar adherencia a la ASTM E-10, al mismo tiempo que permite pruebas ópticas totalmente automatizadas.
Un sistema de detección óptico automático totalmente integrado Brinell puede realizar de forma rápida y precisa todo el proceso de prueba de Brinell de acuerdo con ASTM E10, incluyendo la aplicación de indentación precisa y proporcionar un sistema de análisis de imagen para autofocus, identificar y registrar medidas de dureza y tamaño de sangría. Todo esto, junto con un software flexible y fácil de usar, le da al operador una extensa y abundante capacidad de generar pruebas, completar el análisis y generar reportes. Un operador sólo tiene que localizar la muestra en el probador, y presione el botón de inicio. La sangría es automática, al igual que la rotación de un sistema de revólver o torreta que sitúa el objetivo / microscopio de medición en posición. El enfoque automático y el proceso de formación de imágenes se inicia y los resultados se devuelven en tan sólo 20 segundos.
Las limitaciones pasadas en cuanto al acabado superficial, iluminación, calibración preestablecida, así como el tamaño de píxeles se han mitigado, y están continuamente experimentando mejoras. El resultado es una mayor capacidad y dependencia de «permitir que el instrumento haga el trabajo», lo que contribuye a aumentos sustanciales en el rendimiento y la consistencia, mientras que libera al operador de otras responsabilidades. Con un sistema totalmente integrado, el proceso intensivo en mano de obra, subjetivo y propenso a errores es prácticamente eliminado y reemplazado por un proceso significativamente más preciso y productivo.
Para obtener información adicional sobre preparación de muestras y consumibles metalográficos, envíanos un correo a:
info@mess.com.mx

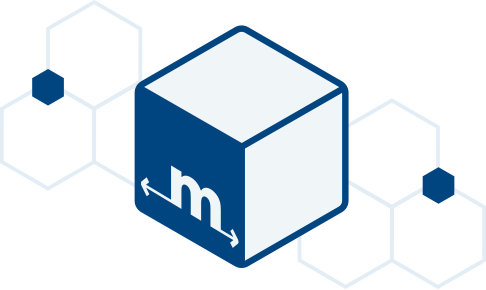